
NewsInformation Center
What is the principle of the fatigue testing machine?
2023/08/04
The principle of a fatigue testing machine is to subject a material or component to cyclic loading in order to assess its fatigue performance and durability. The machine applies repetitive loads to the specimen and measures its response over a specified number of loading cycles. The key principles of a fatigue testing machine are as follows:
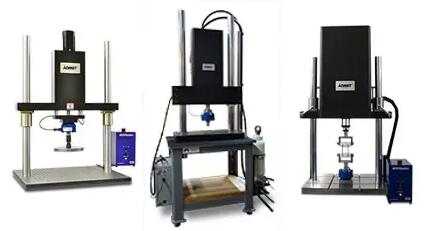
1. Loading Mechanism:
The fatigue testing machine applies cyclic loads to the specimen using various loading mechanisms such as hydraulic, pneumatic, or electromechanical systems. These mechanisms generate controlled forces or displacements that are applied to the specimen.
The fatigue testing machine applies cyclic loads to the specimen using various loading mechanisms such as hydraulic, pneumatic, or electromechanical systems. These mechanisms generate controlled forces or displacements that are applied to the specimen.
2. Specimen Fixturing:
The specimen is securely held within the testing machine to ensure proper alignment and to prevent any unwanted movement during the test. The fixturing mechanism may vary depending on the type of specimen and the desired loading configuration (tension, compression, bending, etc.).
The specimen is securely held within the testing machine to ensure proper alignment and to prevent any unwanted movement during the test. The fixturing mechanism may vary depending on the type of specimen and the desired loading configuration (tension, compression, bending, etc.).
3. Load Control:
The machine controls the magnitude and pattern of the applied load throughout the test. Load control can be achieved through feedback mechanisms, where sensors measure the load or displacement and provide input to the control system for adjustment. This ensures that the desired load profile is maintained accurately.
The machine controls the magnitude and pattern of the applied load throughout the test. Load control can be achieved through feedback mechanisms, where sensors measure the load or displacement and provide input to the control system for adjustment. This ensures that the desired load profile is maintained accurately.
4. Monitoring and Data Acquisition:
The fatigue testing machine is equipped with sensors and transducers to measure various parameters such as load, displacement, strain, and time. These sensors capture data continuously during the test and provide real-time feedback on the specimen's response to cyclic loading. The acquired data is then recorded and analyzed for further evaluation.
The fatigue testing machine is equipped with sensors and transducers to measure various parameters such as load, displacement, strain, and time. These sensors capture data continuously during the test and provide real-time feedback on the specimen's response to cyclic loading. The acquired data is then recorded and analyzed for further evaluation.
5. Test Configuration:
The machine allows for different test configurations depending on the specific requirements of the fatigue test. These configurations include tension-compression, bending, torsion, or multi-axial loading arrangements. The selection of the appropriate test configuration depends on the anticipated loading conditions in the application.
The machine allows for different test configurations depending on the specific requirements of the fatigue test. These configurations include tension-compression, bending, torsion, or multi-axial loading arrangements. The selection of the appropriate test configuration depends on the anticipated loading conditions in the application.
6. Test Control and Analysis:
The fatigue testing machine is typically controlled by a computerized system that enables precise control of the loading parameters and automates the test procedures. The collected data can be analyzed using various techniques such as stress-life (S-N) curves, strain-life (ε-N) curves, or crack growth analysis to evaluate the material's fatigue behavior.
The fatigue testing machine is typically controlled by a computerized system that enables precise control of the loading parameters and automates the test procedures. The collected data can be analyzed using various techniques such as stress-life (S-N) curves, strain-life (ε-N) curves, or crack growth analysis to evaluate the material's fatigue behavior.
Overall, the principle of a fatigue testing machine involves applying controlled cyclic loads to a specimen while continuously monitoring its response. By subjecting materials or components to repetitive loading, engineers can assess their fatigue strength, durability, and potential failure modes, providing important insights for design optimization and ensuring reliable performance in real-world applications.
Previous: What are the different types of UV aging test machines available?
N e x t : Benefits of UV Lamp Test Chambers in Various Industries: An Overview