
NewsInformation Center
Abrasion Testing of Coatings - ASTM D4060 Challenges and Updates
2023/08/08
ASTM D4060 Standard Test Method for Abrasion Resistance of Organic Coatings is one of the most common tests for evaluating the abrasion resistance of coatings. Known as the Taber Test, this test method is used to determine the abrasion resistance of organic coatings such as paints, varnishes, varnishes, powder coatings and many other types of finishes. In addition to the visual aspect of the coating, it often serves a functional purpose (such as corrosion protection). This test method can be used to evaluate the durability and performance of coatings.
How is the ASTM D4060 test performed?
To perform ASTM D4060, organic coatings are applied in uniform thickness to flat, rigid panels using a TABER Abrasion Tester and, after curing, the surface is abraded using rotational friction action under controlled pressure and abrasive action conditions. The test sample mounted on the turntable platform is turned on a vertical axis against the sliding rotation of the two grinding wheels. One grinding wheel rubs outward against the edge of the specimen and the other inward against the center of the specimen. The resulting wear marks form a cross-arc pattern over an area of approximately 30 square centimeters. A vacuum system was used to remove any loose debris created during the test. The grinding wheels were resurfaced with S-11 conditioning discs before each test and after every 500 cycles to standardize the wheel surface. Wear resistance calculations is the weight loss at the specified number of abrasion cycles, the weight loss per cycle, or the number of cycles required to remove a unit amount of coating thickness.
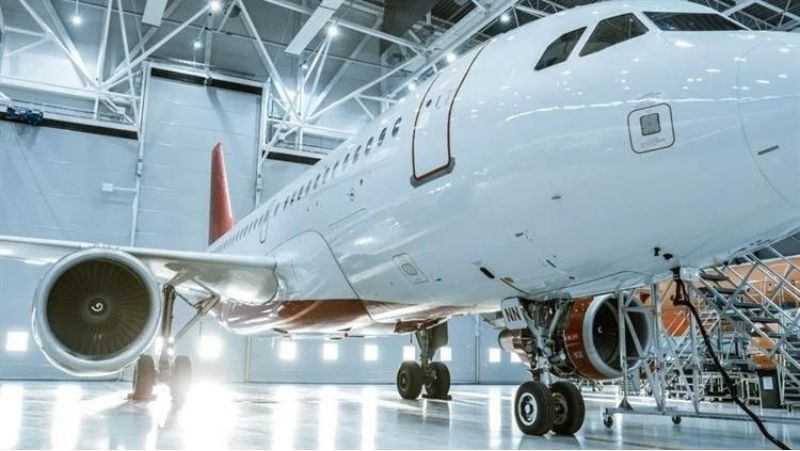
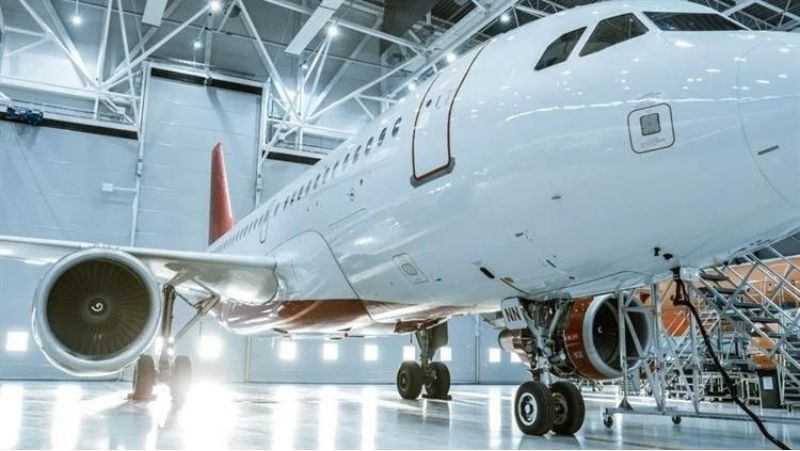
What difficulties have been demonstrated when testing abrasion resistance according to ASTM D4060?
The durability of protective coatings is an important consideration for many different products. This is especially important when selecting coatings that will be subject to vehicular or pedestrian traffic (e.g. parking lots, loading docks, sidewalks, etc.).
To assist in the selection process, architects/consultants rely on test data - especially the abrasion resistance of the coating. This information is usually reported by the paint manufacturer and is based on testing performed according to ASTM D4060. Until recently, this long-established test methods may mislead decision makers.
The data presented in ASTM D4060 Precision and Bias (Table 1) show that the mass loss was more than doubled for the epoxy resins tested compared to the polyurethanes.
In more than 200 project comparisons, epoxy resins and methyl methacrylate (MMA) had the greater mass loss with the CS-17 wheel, while polyurethane coatings had the least mass loss. On its own, this data seems to suggest that polyurethane has better abrasion resistance. However, in field applications, epoxy and MMA have proven to be more durable than 99% of polyurethanes placed on parking lots and other transportation services. In fact, epoxy, MMA, PMMA, and PUMA last twice as long in parking lot traffic.
Why would an abrasion test to ASTM D4060 not provide sufficient testing in this case?
Paint manufacturers' data sheets usually show test results as mass loss due to abrasion or wear index (reported as mass loss per cycle). However, these data may not tell the full story when comparing two coatings.
For example, consider a test performed on two completely different materials—a lead-nickel clad panel and a base polyurethane protective coating. After subjecting both specimens to the same test conditions and number of wear cycles, the mass loss of the lead-nickel clad plate was 800 mg. In comparison, the mass loss of the polyurethane coating was only 33 mg. Based on this information, it is easy to conclude that the polyurethane coating has less mass loss and is therefore more wear-resistant. But is that really the case?
What if you also knew that the thickness of the lead sheet varied by 0.1 mils and the thickness of the polyurethane coating varied by 2.0 mils? With this additional information, you will quickly realize that more material was removed from the polyurethane sample, This means it is actually less wear resistant!
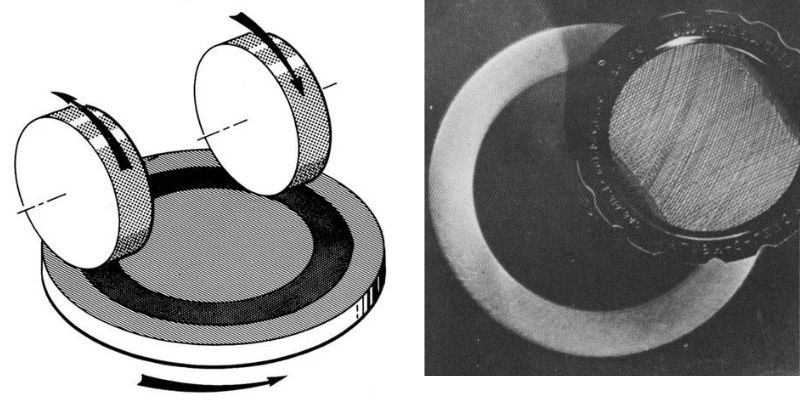
For many trafficable coatings, it is important to realize that coatings with dense fillers generally exhibit greater mass loss than similar coatings without fillers, but in some cases caused by abrasion Thickness loss is low. ASTM D4060 results are usually reported as mass loss. But dividing mass loss by specific gravity provides a better relationship for comparison.
Given this new information, what tests were done to investigate wear?
Tremco Inc. CS&W began a single lab study in November 2018 that evaluated more than 1,000 test samples, including different polyurethane formulations; epoxy resins; mixed martial arts; and traffic coatings. All samples were tested in accordance with ASTM D4060, but additional parameters were included to help calculate researchers' estimates of coating life.
What other factors were found to affect wear testing in accordance with ASTM D4060?
Wear debris containing higher point density particles can cause three-body wear, which can lead to cracking of the coating if not removed by a vacuum suction system. During the research, it was observed that certain grinding wheels increased the number of wear particles present during the test, which further increased the wear rate.
An increase in the surface temperature of the test samples was also observed when fillers such as 3D crystal structures or metals were included in the coating. Under slow thermal microscopic video, the epoxy in contact with the CS-17 (or CS-10) wheel generates heat that binds fine epoxy particles, and the vacuum cannot move quickly enough from intimate contact with the specimen Remove these fine epoxy resin particles from the grinding wheel.
Other parameters were also found to affect the wear rate, and in many cases the coating caused greater wear on the Taber wheel. Certain epoxy and MMA materials that have a higher hardness value or coefficient of friction than the wheel may cause the wheel to break down more quickly, especially if the coating formulation contains fillers or aggregates such as silica, metal oxides, or other high point dense particles). This "counterattack" is affected by particle size, number and type of particles.
The coefficient of friction (COF) between the coating and the grinding wheel also affects the results. In some tests, it was observed that the COF between the sources of friction (CS-10 or CS-17 wheels) would rise or fall as the wheel broke surface tension - the point where the wheel loses gloss and is the inside of the abraded coating.
Some coatings have entrapped air bubbles that become exposed after 50 – 100 wear cycles, which may alter the mass loss during comparative testing. With some flexible urethane coatings, the more air is entrained, the less mass is lost as the wheel travels on a reduced solids content.
For highly reactive materials such as epoxies, the interaction between wear debris and air entrainment is significantly different. With hard epoxy coatings, the abrasion process tends to shatter the very hard particles that make up the coating, which can lead to more wear debris and higher mass loss than expected in use.
ASTM D4060 version update
The 2019 edition of ASTM D4060 includes a note stating that when comparing the abrasion resistance of coatings with different specific gravity, the specific gravity correction for each coating should be applied to the mass loss to give a true measure of the comparative abrasion resistance.
After calculating the wear index or mass loss, the result is divided by the specific gravity of the coating. The use of this correction factor provides the wear index or mass loss relative to the volume loss of the material to which it is applied.
Previous: How can I contact a manufacturer of zipper testing equipment?
N e x t : What materials improve the safety of burning car interiors?