
NewsInformation Center
What is the use of a scratch/shear tester?
2023/08/24
Scratch/shear tester is a specialized device used to evaluate the scratch resistance and shear strength of various materials. It provides quantitative measurements and assessments of a material's response to scratching or shearing forces. The information obtained from this type of testing is valuable in industries such as automotive, aerospace, electronics, coatings, plastics, and material science. In this response, I will explain the purpose, working principle, applications, and benefits of a scratch/shear tester.
Purpose of a Scratch/Shear Tester:
The main purpose of a scratch/shear tester is to assess the durability, mechanical properties, and surface performance of a material when subjected to scratching or shearing actions. It helps manufacturers and researchers understand how a material will perform during its intended application or under simulated real-life conditions. By quantifying scratch resistance and shear strength, design improvements can be made, and materials can be selected or modified to enhance product performance and customer satisfaction.
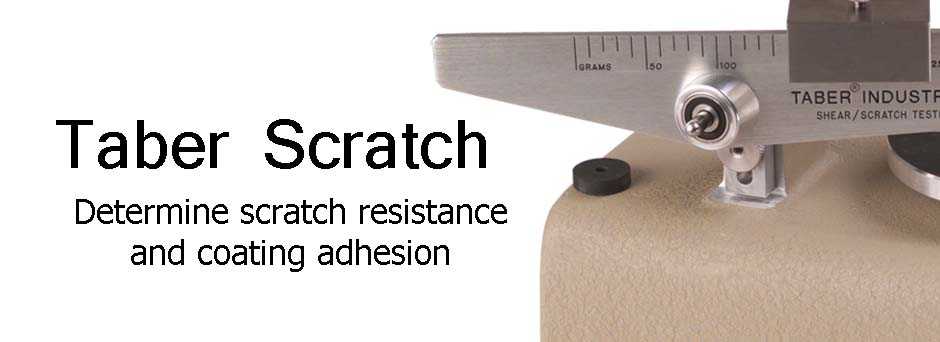
Working Principle:
A scratch/shear tester typically consists of a stylus or indenter made of a hard material, such as diamond or tungsten carbide, which is applied to the surface of the test material. The indenter is mounted on a movable arm or stage, and a controlled load is applied as it moves across the sample. The applied load, speed, and stylus geometry are adjustable parameters that can be tailored to specific testing requirements.
During a scratch test, the stylus is drawn across the sample surface in a linear or rotational motion at a specified speed and under a controlled load. The force required to initiate material deformation, create scratches, or cause failure is measured and recorded. The scratch resistance is evaluated by analyzing the depth and width of the scratch, as well as any associated surface damage.
In shear testing, the stylus is used to apply a lateral force to the surface of the test material. The force required to induce shear or remove a portion of the material is measured, providing information about the material's resistance to shearing or cutting.
Applications of a Scratch/Shear Tester:
1. Coatings and Paints:
Scratch resistance testing helps evaluate the durability, adhesion, and protective properties of coatings and paint finishes. It is essential in industries such as automotive, aerospace, and consumer goods.
Scratch resistance testing helps evaluate the durability, adhesion, and protective properties of coatings and paint finishes. It is essential in industries such as automotive, aerospace, and consumer goods.
2. Plastics and Polymers:
Scratch/shear testing assesses the surface properties and abrasion resistance of plastic materials, including films, molded parts, and composite materials. It aids in material selection, product development, and quality control.
Scratch/shear testing assesses the surface properties and abrasion resistance of plastic materials, including films, molded parts, and composite materials. It aids in material selection, product development, and quality control.
3. Metals and Alloys:
The scratch and shear strength of metallic materials are evaluated to determine their resistance to wear, indentation, or deformation. This information is crucial for designing components subjected to friction, such as bearings, gears, or cutting tools.
The scratch and shear strength of metallic materials are evaluated to determine their resistance to wear, indentation, or deformation. This information is crucial for designing components subjected to friction, such as bearings, gears, or cutting tools.
4. Electronic Displays:
Scratch resistance testing is essential for assessing the durability and performance of displays, touchscreens, and protective or anti-reflective coatings used in electronic devices.
Scratch resistance testing is essential for assessing the durability and performance of displays, touchscreens, and protective or anti-reflective coatings used in electronic devices.
5. Medical Devices:
Scratch/shear testing is used to evaluate the biocompatibility and mechanical properties of medical implants, prosthetics, and surgical instruments. It helps ensure their safety and effectiveness during use.
Scratch/shear testing is used to evaluate the biocompatibility and mechanical properties of medical implants, prosthetics, and surgical instruments. It helps ensure their safety and effectiveness during use.
6. Surface Engineering:
Scratch/shear tests aid in the development and evaluation of surface treatments, coatings, and modifications aimed at improving the wear resistance, adhesion, or frictional properties of materials.
Scratch/shear tests aid in the development and evaluation of surface treatments, coatings, and modifications aimed at improving the wear resistance, adhesion, or frictional properties of materials.
Benefits of a Scratch/Shear Tester:
1. Quality Control:
A scratch/shear tester provides objective and quantitative data for assessing material quality, identifying defects, and ensuring product consistency.
A scratch/shear tester provides objective and quantitative data for assessing material quality, identifying defects, and ensuring product consistency.
2. Material Selection:
By comparing the scratch resistance and shear strength of different materials or coatings, engineers can select the most appropriate choices for a specific application or environment.
By comparing the scratch resistance and shear strength of different materials or coatings, engineers can select the most appropriate choices for a specific application or environment.
3. Product Development:
Scratch/shear testing facilitates the optimization of material formulations and product designs, leading to improved performance, durability, and customer satisfaction.
Scratch/shear testing facilitates the optimization of material formulations and product designs, leading to improved performance, durability, and customer satisfaction.
4. Performance Evaluation:
Testing material responses to scratches and shear forces enables manufacturers to predict and evaluate how a product will perform under real-life conditions, helping to avoid premature failures.
Testing material responses to scratches and shear forces enables manufacturers to predict and evaluate how a product will perform under real-life conditions, helping to avoid premature failures.
5. Validation and Compliance:
Scratch/shear testing can validate material specifications, compliance with industry standards or regulations, and the suitability of materials for specific applications.
Scratch/shear testing can validate material specifications, compliance with industry standards or regulations, and the suitability of materials for specific applications.
6. Research and Innovation:
Scratch/shear testers enable researchers to investigate new materials, surface treatments, or manufacturing techniques, advancing the development of innovative products.
Scratch/shear testers enable researchers to investigate new materials, surface treatments, or manufacturing techniques, advancing the development of innovative products.
In conclusion, a scratch/shear tester is a valuable tool for evaluating the scratch resistance and shear strength of various materials across multiple industries. By quantifying material responses to scratching and shearing forces, manufacturers and researchers can make informed decisions, enhance product performance, and ensure customer satisfaction.
Previous: What is the best Uv lamp aging test chamber?
N e x t : What is the critical load in scratch test?