
NewsInformation Center
What is the testing principle of the air permeability tester?
2021/02/01
The air permeability tester is one of the family of gas permeability testers, which is suitable for the air permeability of various textiles including industrial fabrics, nonwovens and other breathable products such as sponges. And the detection of high permeability materials such as paper. The basic information is applicable to the determination of air permeability of various textile fabrics, including industrial fabrics, nonwovens and other breathable materials.
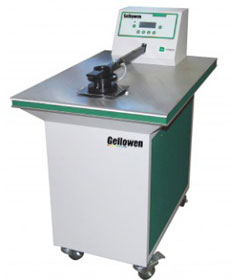
Air permeability tester features:
1. The instrument has its own temperature control function, which can simulate the condition of the product in the actual environment, and can meet various requirements of material permeability test within the temperature range.
2. It has a unique fitting function, which can measure the air permeability, air permeability coefficient, solubility coefficient and diffusion coefficient of materials at -273℃~+200℃, and meet the requirements of testing and evaluating the air permeability of plastic films under special application conditions such as high and low temperature.
3. Computer control, full-automatic test.
4. Measurement of transmittance, solubility, diffusion and permeability coefficient.
5. Proportional and fuzzy test process judgment mode.
6. Expandable test of toxic and explosive gases.
7. Software-configurable expansion of measuring range.
8. Rapid calibration of standard membrane.
9. Network transmission interface supports centralized management of local area network data and Internet information transmission.
Application industry: Widely used in food, medicine, packaging, plastic, industry, electronics, energy and other industries, suitable for plastic film, composite film, paper-plastic composite packaging, solar back plate, sheet, composite material, aluminum plating film, co-extruded film and other films, aluminum foil, sheet materials and packaging containers such as bottles, bags, cans and boxes of plastic, rubber, paper, glass and metal materials.
Test principle: place the pre-processed sample between the upper and lower test chambers and clamp it. First, vacuum the low-pressure chamber (lower chamber), then vacuum the whole system. When the specified vacuum degree is reached, close the lower chamber, fill the high-pressure chamber (upper chamber) with a certain pressure of test gas, and ensure that a constant pressure difference (adjustable) is formed on both sides of the sample, so that the gas will permeate from the high pressure side to the low pressure side under the action of pressure difference gradient.
Operating environment:
1. The instrument should be placed on a flat and stable platform (or foundation).
2. There is no strong magnetic field and no vibration source around the instrument.
3. The indoor atmosphere is free of corrosive medium and large particle dust, and the airflow is stable.
4. Environment: temperature 20 3℃, humidity RH: ≤ 65%.
5. The power supply AC 220 V 10 V, 50Hz is used, and the grounding is good. For areas with large fluctuation of external power supply, it is recommended to use power regulator (AC 220 1% 2 kW).
Debugging:
1. The instrument should be leveled before working. The specific operation is to rotate the adjustable foot to level the instrument.
2. Check whether the fixed value ring of the sample is tightened and whether the air seal ring is close to the two combination surface.
3. Check whether the pressure head can be controlled to move up and down flexibly.
4. Check whether the suction hose is tightly connected with the flow cylinder and the suction fan.
5. Check whether the door cover and door lock on the flow cylinder can be tightly closed.
6. Check whether the printer is online correctly.
7. Calibration
8. Check whether the instrument leaks: replace the calibration plate with a non-perforated plate for testing. If the air permeability screen displays 0 (the allowable runout is below 10Pa), it means no air leakage; otherwise, some parts of the instrument leak and should be checked and adjusted.
Fold and edit the operation steps of this paragraph:
1. Prepare the sample as required and cut it to the specified size.
2. Select the sample fixing ring and install it on the instrument.
3. Select the nozzle.
4. Turn on the instrument power supply.
5. Set parameters.
6. Press the start button to start the instrument.
7. The instrument automatically compresses the sample and starts the test. When the set pressure difference is reached, the sample is automatically released, and the instrument automatically converts the test result and stops.
8. Test the next sample until the effective number of tests meets the requirements (the number of tests is currently displayed on the number display screen), and perform data processing according to GB/T 5453-97.
9. The test results can be observed on the air permeability/differential pressure display screen or printed.
10. After the test is finished, turn off the power supply, clean the instrument and accessories, and remove the fixed value ring and put it in the spare parts drawer.
Matters needing attention:
1. The instrument is of high precision, and collision and violent turbulence are strictly prohibited during moving and transportation.
2. The instrument has been calibrated when leaving the factory, and non-professionals should not repair the internal devices of the instrument.
3. Instrument accessories (nozzle, nozzle seat, orifice plate and sample setting ring) are directly related to the test accuracy, so it is not allowed to wipe them directly with a rag. If there is any contamination, the dust on the surface should be blown by the ear-blowing ball.
4. During the test, do not touch the sample, so as not to affect the air permeability of the sample.
5. The nozzle diameter should be selected according to the air permeability of the sample. For the sample whose air permeability is unclear, it is necessary to test it several times more accurately to reflect the air permeability of the sample.
6. The filter screen in the airflow measuring cylinder should be cleaned regularly depending on the frequency of use.
7. If the instrument is tested for a long time, and the pressure difference is unstable and the noise of fan is too large continuously, stop the machine to check the air tightness of each component or whether the selected test piece is within the range.
8. For samples with different thicknesses, the position of the pressure head of the sample should be adjusted so that it can press the sample tightly.
9. Instrument testing is related to air pressure, so it is recommended to proofread it once every working day, and the instrument proofreading should be carried out by special personnel.
10. There are precision sensing elements in the air flow measuring cylinder, so the action should be gentle when changing nozzles and cleaning, so as to avoid accidents.
11. The air tightness of each seal joint directly affects the test accuracy, so care should be taken for contamination, deformation and damage.
12. Select nozzle number: It is recommended to make the dynamic pressure difference fall within the range of 600~3000Pa to obtain more stable test results.
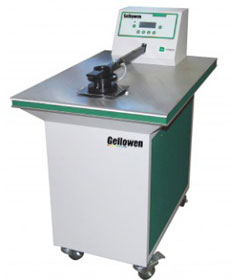
Air permeability tester features:
1. The instrument has its own temperature control function, which can simulate the condition of the product in the actual environment, and can meet various requirements of material permeability test within the temperature range.
2. It has a unique fitting function, which can measure the air permeability, air permeability coefficient, solubility coefficient and diffusion coefficient of materials at -273℃~+200℃, and meet the requirements of testing and evaluating the air permeability of plastic films under special application conditions such as high and low temperature.
3. Computer control, full-automatic test.
4. Measurement of transmittance, solubility, diffusion and permeability coefficient.
5. Proportional and fuzzy test process judgment mode.
6. Expandable test of toxic and explosive gases.
7. Software-configurable expansion of measuring range.
8. Rapid calibration of standard membrane.
9. Network transmission interface supports centralized management of local area network data and Internet information transmission.
Application industry: Widely used in food, medicine, packaging, plastic, industry, electronics, energy and other industries, suitable for plastic film, composite film, paper-plastic composite packaging, solar back plate, sheet, composite material, aluminum plating film, co-extruded film and other films, aluminum foil, sheet materials and packaging containers such as bottles, bags, cans and boxes of plastic, rubber, paper, glass and metal materials.
Test principle: place the pre-processed sample between the upper and lower test chambers and clamp it. First, vacuum the low-pressure chamber (lower chamber), then vacuum the whole system. When the specified vacuum degree is reached, close the lower chamber, fill the high-pressure chamber (upper chamber) with a certain pressure of test gas, and ensure that a constant pressure difference (adjustable) is formed on both sides of the sample, so that the gas will permeate from the high pressure side to the low pressure side under the action of pressure difference gradient.
Operating environment:
1. The instrument should be placed on a flat and stable platform (or foundation).
2. There is no strong magnetic field and no vibration source around the instrument.
3. The indoor atmosphere is free of corrosive medium and large particle dust, and the airflow is stable.
4. Environment: temperature 20 3℃, humidity RH: ≤ 65%.
5. The power supply AC 220 V 10 V, 50Hz is used, and the grounding is good. For areas with large fluctuation of external power supply, it is recommended to use power regulator (AC 220 1% 2 kW).
Debugging:
1. The instrument should be leveled before working. The specific operation is to rotate the adjustable foot to level the instrument.
2. Check whether the fixed value ring of the sample is tightened and whether the air seal ring is close to the two combination surface.
3. Check whether the pressure head can be controlled to move up and down flexibly.
4. Check whether the suction hose is tightly connected with the flow cylinder and the suction fan.
5. Check whether the door cover and door lock on the flow cylinder can be tightly closed.
6. Check whether the printer is online correctly.
7. Calibration
8. Check whether the instrument leaks: replace the calibration plate with a non-perforated plate for testing. If the air permeability screen displays 0 (the allowable runout is below 10Pa), it means no air leakage; otherwise, some parts of the instrument leak and should be checked and adjusted.
Fold and edit the operation steps of this paragraph:
1. Prepare the sample as required and cut it to the specified size.
2. Select the sample fixing ring and install it on the instrument.
3. Select the nozzle.
4. Turn on the instrument power supply.
5. Set parameters.
6. Press the start button to start the instrument.
7. The instrument automatically compresses the sample and starts the test. When the set pressure difference is reached, the sample is automatically released, and the instrument automatically converts the test result and stops.
8. Test the next sample until the effective number of tests meets the requirements (the number of tests is currently displayed on the number display screen), and perform data processing according to GB/T 5453-97.
9. The test results can be observed on the air permeability/differential pressure display screen or printed.
10. After the test is finished, turn off the power supply, clean the instrument and accessories, and remove the fixed value ring and put it in the spare parts drawer.
Matters needing attention:
1. The instrument is of high precision, and collision and violent turbulence are strictly prohibited during moving and transportation.
2. The instrument has been calibrated when leaving the factory, and non-professionals should not repair the internal devices of the instrument.
3. Instrument accessories (nozzle, nozzle seat, orifice plate and sample setting ring) are directly related to the test accuracy, so it is not allowed to wipe them directly with a rag. If there is any contamination, the dust on the surface should be blown by the ear-blowing ball.
4. During the test, do not touch the sample, so as not to affect the air permeability of the sample.
5. The nozzle diameter should be selected according to the air permeability of the sample. For the sample whose air permeability is unclear, it is necessary to test it several times more accurately to reflect the air permeability of the sample.
6. The filter screen in the airflow measuring cylinder should be cleaned regularly depending on the frequency of use.
7. If the instrument is tested for a long time, and the pressure difference is unstable and the noise of fan is too large continuously, stop the machine to check the air tightness of each component or whether the selected test piece is within the range.
8. For samples with different thicknesses, the position of the pressure head of the sample should be adjusted so that it can press the sample tightly.
9. Instrument testing is related to air pressure, so it is recommended to proofread it once every working day, and the instrument proofreading should be carried out by special personnel.
10. There are precision sensing elements in the air flow measuring cylinder, so the action should be gentle when changing nozzles and cleaning, so as to avoid accidents.
11. The air tightness of each seal joint directly affects the test accuracy, so care should be taken for contamination, deformation and damage.
12. Select nozzle number: It is recommended to make the dynamic pressure difference fall within the range of 600~3000Pa to obtain more stable test results.
Previous: Mask BFE Tester detects whether N95 mask meets the standard
N e x t : Attention of static electricity tester instrument features