
NewsInformation Center
How to choose the best Insulation Resistance Tester?
2023/01/06
To detect current leakage and poor or damaged insulation that can cause arc faults, circuit blowouts, and shock or fire hazards, the Insulation Resistance Tester applies a high voltage, low current DC charge to wires and motor windings to measure their resistance. What is an insulation resistance test?
The definition of an insulation resistance test is a test used to measure the total resistance between any two points separated by electrical insulation. The test can be defined as a test for measuring the resistance between any two locations. This check is also known as the "Megger test".
Therefore, the purpose of this test is to measure the effectiveness of a dielectric or insulator in restricting the passage of electrical current. Therefore, infrared (IR) testing is very useful not only in confirming the insulation quality of the product when it is produced, but also very helpful in verifying the insulation quality when the product is used for a long time.
Why do I need an insulation resistance test?
Electricity must pass through conductive wires to reach its destination, but some energy is lost in the process. We must check the insulation to see if any leakage has occurred.
This is because stray currents can be a significant risk. These tests must be carried out to ensure that no one is harmed.
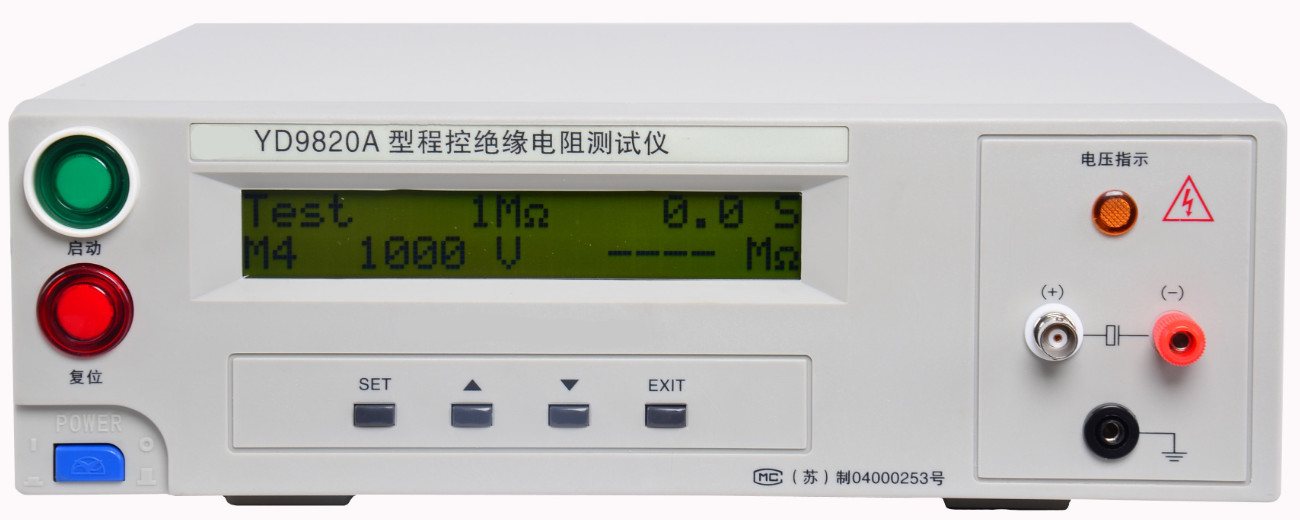
Such tests are needed to ensure the reliability of appliances and to ensure their safety. This testing allows one to assess whether the electrical equipment is in good operating condition and also to predict how long the insulation will be effective.
When repairing or installing new electrical equipment, it is vital to test the insulation. This is because testing insulation ensures that it is in good working order.
How do I choose the best Insulation Resistance Tester?
There are six factors to consider when choosing the best Insulation Resistance Tester, including the following.
What equipment needs to be tested?
In the first stage, you will want to list all the typical machines that will inevitably require an Insulation Resistance Test. Record the target number of insulation resistance tests per year and the voltage rating of the equipment (located on the nameplate). Indicate the test voltage required for Insulation Resistance TesterWB2681A, the nominal voltage is a useful starting point.
It may be surprising to anticipate the number of insulation resistance tests per year. As the number of tests to be carried out increases, so does the significance of the general quality, durability and convenience characteristics of the test instrument.
What are the voltage requirements?
The manufacturer's recommended DC insulation resistance test voltage should be used to determine the output test voltage to be applied to the equipment. In the absence of a defined test voltage, standard industry values should be used instead.
The required output test voltage must be provided by the Insulation Resistance Tester of your choice. There are various Insulation Resistance Testers on the market, some can only provide test voltages up to 1,000 V dc, while others can provide 5,000 V dc or more. Where do I need to test?
Choosing the optional features of the Insulation Resistance Tester may help to think about the test environment and other potential applications for the tool. For example, if a single device can perform both digital multimeter and insulation resistance tests, this can be a significant time saver.
It is inconvenient to carry a digital multimeter for voltage testing and Insulation Resistance Tester because it is necessary to ensure that all circuits and equipment are disconnected before connecting the tester.
These are some of the issues to consider when planning your test environment.
1) If you are going to use the Insulation Resistance Tester, ask yourself, "Will it be used for troubleshooting, preventive maintenance, or both?"
2) "Will the test equipment only be used in the factory or will it also be used on the shop floor?"
Different insulation resistance tests are available in different sizes and portability.
What is your understanding of insulation resistance testing?
The insulation resistance test assigns a numerical value to the state of the conductor insulation and internal insulation of various electrical equipment to qualitatively evaluate its overall condition.
Applying a DC voltage to the wire or device under test is the first step in performing an insulation resistance test. A small amount of current escapes from the test instrument and enters the conductor, where it begins to charge the insulation.
Capacitive charging current is the name for this current and it can be seen on the front of the meter.
When the charging current starts to increase, the reading on the front of the meter will reflect a low value of the measured resistance. Imagine when electrons start flowing into the insulating layer and are stored there.
It will drop the megohm value proportionally to the amount of current drawn from the test setup. If the insulation is of good quality, it will soon become charged and the meter reading will start to stabilize at a higher megohm value.
Sink current, also known as polarization current, is the current that flows subsequently. The degree of contamination in an insulator is directly proportional to the amount of electricity absorbed.
For example, if moisture is present in an insulator, the current drawn will be greater, indicating that the insulator has a lower resistance value. However, it is important to remember that it takes more time to build up this sink current than the capacitive charge current.
Therefore, an Insulation Resistance Tester WB2681A run for too short a time will observe capacitive charging current and will not begin to show signs of impurities in the insulation.
In summary, the current called leakage current is the current that flows through damaged insulation and into uncharged metal parts. In most cases, this current is taken into account during insulation resistance testing.
However, it must also include sinking or polarizing currents for more precise maintenance and troubleshooting.
Do you measure polarisation currents?
The Insulation Resistance Tester requires more time to run due to the increased time required for the polarisation current to build up. This evaluation usually takes five minutes. Take a reading from the Insulation Resistance Tester after one minute and again after ten minutes to see the level of contamination and general insulation condition.
To obtain the polarisation index, divide the first minute's reading by the tenth minute's reading. It is recommended that field reading test results and polarisation index values are tracked as part of a regular maintenance schedule. It should always compare the latest value with the historical average. Never have a polarisation index value below 1.0.
Do you measure leakage currents?
Those testers that obtain this data automatically should be used preferentially in industrial environments. However, all Insulation Resistance Testers will display the leakage current and provide information for estimating insulation contamination.
During the leakage test, the test voltage is applied to the component for one minute before resistance measurements are taken to determine the leakage current. The spot reading test refers to this particular test.
The field reading test is the gold standard for determining the insulation leakage current as it allows the capacitor charging current to stabilise. The field reading test should be used as the basis for determining the minimum insulation resistance value in megohms.
Standard International Group (HK) Limited offers the best Insulation Resistance Tester according to your requirements.
Previous: Taber abrasion tester speed setting method
N e x t : Water-cooled xenon lamp aging test chamber with broadband and narrowband irradia